Features of furniture additive machines, their types and use
If you are already engaged or just want to start producing furniture, then a drilling and additive machine will probably come in handy. It will help to precisely drill the necessary holes with which the elements will connect. If the filler machine for furniture, makes parts according to pre-drawn drawings, then you will get the best result, it will take less time and effort to work, and the manufactured furniture will be reliable and beautiful. Such a machine, of course, is expensive. This is a high-tech unit, it is not needed for one stool or table, but it is extremely necessary for small production.
Scope of use
Do-it-yourself additives are needed to drill accurate and accurate holes at specific points. They will not have torn wood fibers or any chips. High-quality equipment samples allow this process to be carried out as quickly and almost completely as possible to get low-quality workpieces. When designing furniture, any parts of it are calculated so that they are in a place previously designed for them, any deviations make it difficult to assemble the finished product, and sometimes make it impossible.
The operation of the additive machine occurs on an aggregate basis. This means that several similar devices mounted on the head work simultaneously.
The permissible error for this equipment is 0.4 mm by 64 cm.
Varieties of models
On the additive machine, several similar tools immediately perform their functions - drilling units, countersinks, which are mounted in the head with several spindles.
By appointment, this equipment is divided into:
- Universal furniture machines;
- Specialized equipment;
- Special mechanisms.
Universal equipment - designed for the complete preparation of holes, from drilling to complete processing by other devices. They are often used in the serial production of furniture, they are able to perform many functions. Small, low-power models are for beginner enthusiasts. Specialized device - designed for conveyor processing of necessary parts. At the same time they are capable of processing a certain number of holes. You can customize for different operations. This category includes most of the filler equipment. Special mechanisms - designed only for processing workpieces of a specific configuration. It is impossible to reconfigure them independently for other operations.
The number of spindles and traverses is distinguished by mechanisms:
- Drilling and additive and semi-automatic;
- Positional additives;
- Programmable drilling and additive;
- Additive mechanisms for loops.
The best end result of using these mechanisms can only be obtained by understanding the features of its design and operation.
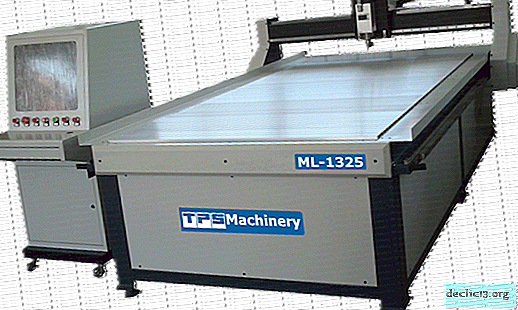
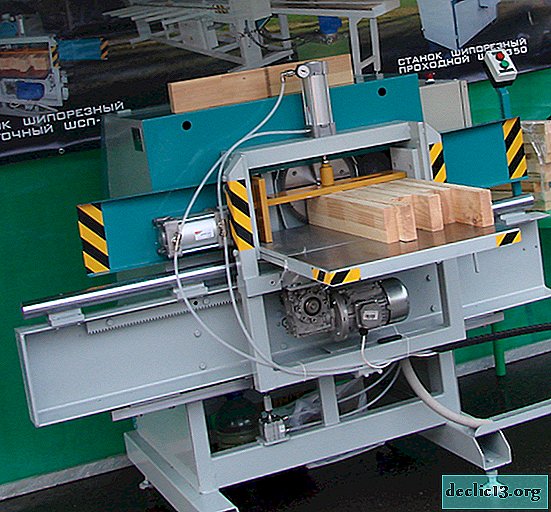
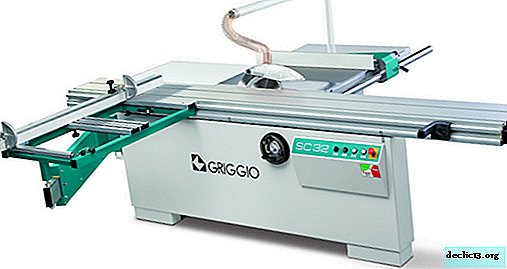
Single head gears
In such a machine, the workpiece is clamped by clamps on the countertop in accordance with the indications of the guide line. Thus, the workpiece is correctly positioned relative to the tools. When the engine is running, the head moves to the workpiece. The mechanism does its job, and the operator, using the remote control, releases the clamps and changes the workpiece.
The versatility of the installation is achieved by moving the spindles 90 degrees. This feature is used to select grooves and to process beveled sides. In the countertop create voids for moving the drilled bottom of the workpiece. Such equipment is successfully used in small organizations with a small flow of workpieces.
Multi-head gears
Among the working tools of this equipment, various devices are used - all kinds of heads for drilling material, and one for finishing the edge of the workpiece. On the bed there is a support necessary for fixing the workpiece in the desired position. The workpiece is placed on special slats and clamped with clamps. During engine operation, several heads function simultaneously. This is expensive equipment, it additionally has control mechanisms, speed control and position controllers for the part.
Differences of machines with several spindles from installations with one spindle:
- The location of the heads is regulated by an electronic device, for this reason the parts are processed with high accuracy, additional adjustments are carried out quickly;
- You can immediately process 2 planes, the work is performed with great accuracy and faster. For another run of several workpieces of the same type, there is no need to readjust the unit;
- Vertical heads can make holes at the required angle;
- Additionally, on the base table there are devices for replacing parts that free a person from manual work. This equipment belongs to positional walk-through installations. They are often used in the conveyor production of furniture. In this case, the machines process the part when moving along the conveyor, this application significantly saves time and completely eliminates the need to perform manual work.
The bulk of industrial equipment belong to this type.
Drill head
Each filler has an element called a drill head. It contains spindles located at an equal distance. This is standard equipment for the manufacture of furniture, it must be included in the kit by all manufacturers of filler machines. Only special-purpose units, for example, those that prepare holes for fastening facade hinges, can only differ. The drilling characteristics may vary, depending on the properties of the loops.
The movement from the electric motor to the head is transmitted through gears that are located in the head. Depending on the number of spindles used, the head can be powered by 2 electric motors. Such a device is used to rotate the spindles in opposite directions. In this case, you can use drills with both left and right threads.
How to do it yourself
The disadvantages of small drilling mechanisms are practically invisible, because in this case it is not necessary to produce many details. And the simplest equipment can prepare accurate and even holes that allow you to make durable and high-quality furniture. Machine tools for the manufacture of furniture, made independently, have their own advantages and disadvantages.
They are good in that:
- The devices are easy to use;
- They have a simple design, for work and maintenance you do not need to have special knowledge;
- You can make holes without obvious defects;
- If necessary, you can increase their productivity;
- Low cost;
- For installation and operation of the unit does not need a lot of space, enough of a small part of the desktop.
However, homemade machines also have disadvantages:
- During operation, only one cutting tool is used;
- Low productivity;
- You cannot perform many operations; additional mechanisms are needed to process different parts;
- No automation;
- It is not possible to turn on different modes.
A reasonable question arises - what versions of a home-made additive mechanism may be, and how to make it. With CNC, it is undoubtedly impossible to make this device at home, but a high-quality albeit a simple furniture machine can be made.
Photographic enlarger as a machine
You can make a convenient home-made filler machine from an old household photo enlarger. Now this device is almost never used, for this reason its parts are often used for various homemade products.
The photo enlarger is used as the functional basis of the design. Most importantly, he has a convenient desktop, with a securely fixed vertical stand, which is equipped with a special mechanism. From the magnifier dismantle the casing. Instead, an electric motor and a chuck for attaching a drill are attached. Most often, the engine is mounted on a plate of a photographic enlarger carriage using clamps. You can use the mixer motor as an electric drive. For our purpose, its power is quite enough, it is small in size and often equipped with a device for changing speeds. A chuck is attached to the axis of the engine, which can clamp drills up to 6 mm in diameter.
Such a machine for manufacturing furniture allows you to partially adjust it by changing the position of the vertical axis along which the cartridge and the drill clamped in it move. And although it does not have the same characteristics as factory models, it will cost almost nothing and will be able to perform simple tasks.
Making a machine from an electric drill
A home-made drilling machine can be made very quickly from a drill, you only need to choose the right parts. It is suitable for carpentry work, some craftsmen even connect CNC to it.
According to the required size, a segment of organic glass is prepared, it will be required for the manufacture of the base of the machine. Then racks and holes for clamps are made, which secure the engine. To make a productive machine, you need a powerful electric drill. Using a drill makes it possible to refuse to search for a suitable cartridge.
But the most difficult thing in this design is to make a durable and reliable movable base. You can find a ready-made lifting table, or use a mobile support on which the electric drill is securely attached. But a small problem appears - the vibration that needs to be eliminated.
The drill must be mounted on a rack with mounting brackets. After that, you need to test the resulting design. We start the drill, switch it to the highest speed and make sure that there is no vibration, if it does, then you will need to strengthen the rack. After that, you can mount the lift table.
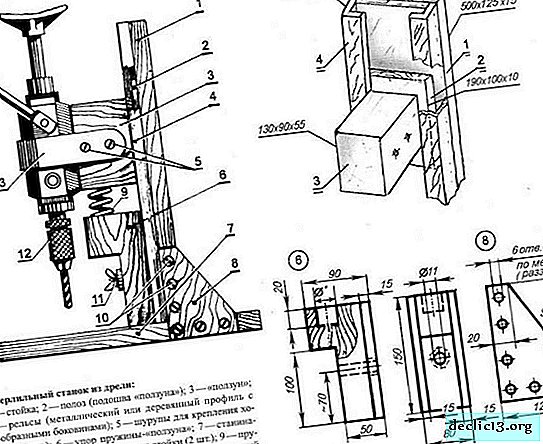
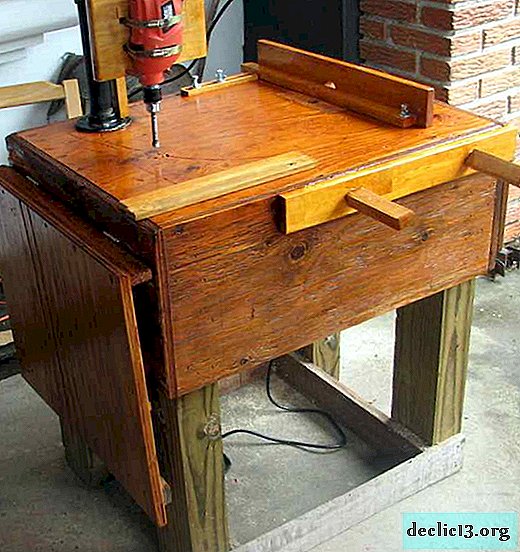
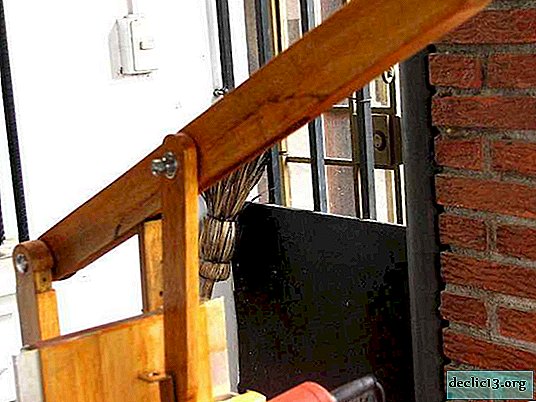
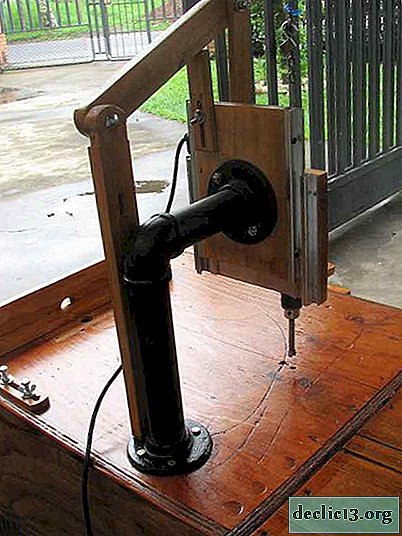
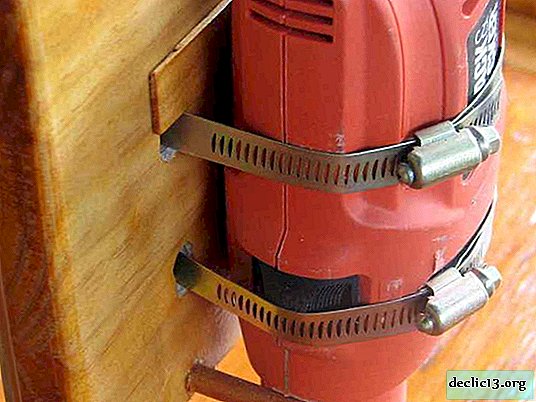
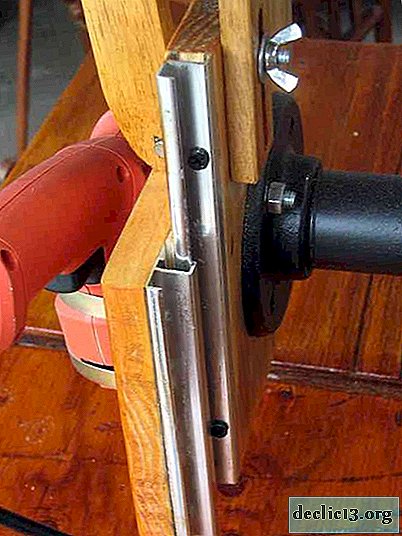
Additive machine washing machine parts
An asynchronous motor, removed from the drum of an old washing machine, allows you to make a more efficient machine than an electric drill. Do not forget that the mass of a productive electric motor is higher than that of a drill. For this reason, you have to think about making a solid base and a reliable stand.
The motor must be placed as close as possible to the upright. And here the difficulty arises - the stand and engine located next to each other reduce the dimensions of the part that can be machined, for this reason it will be necessary to move the cartridge further, and this will require a belt drive.
To independently make such a machine, you need such parts:
- Gear
- Find 2 bearings of the same size;
- Specially machined shaft;
- Pick up 2 tubes into which the bearings fit tightly;
- Clamping ring.
On a lathe, a shaft is machined, on which bearings and a pulley are tightly mounted. Bearings clog into a metal tube. Everything should be as tight as possible so that vibration does not appear. In the future manufacturing of the filler machine is made, as well as the device of the electric drill.